Last Updated on May 5, 2022
If you drive a conventional car, it will likely have five lug nuts (or bolts) at each wheel (some models only have four). These twenty fasteners could be the most important ones on your entire car. That’s because if five of them on any wheel break or come off while you’re driving, you will most assuredly have an extremely troubling experience.
Happily, the scenario I have described is extremely rare. And that is a credit to the automotive engineers who design these fasteners and how they are used to attach your wheels. A big piece of the designing of these fasteners includes making them some of the strongest nuts and bolts on your car.
Sometimes, however, when a flat tire occurs or you just want to rotate the tires, a lug nut will have seized and cannot be removed. It just won’t budge. And on rare occasions, the lug nut is rusted and this corrosion makes removal nearly impossible.
In other cases, surface damage allows the flats on the lug nut to round off as you struggle to remove it. In this article we will discuss what you can do to resolve these problems.
Conventional Lug Nuts vs. Lug Bolts
We’re going to focus on problems with conventional lug nuts screwed on to wheel studs. However, several brands of European cars use lug bolts which screw into the wheel hub. BMW, Audi and Volkswagen are examples.
Some of the techniques discussed here can work for lug bolts as well. This will be noted in the appropriate sections.
Related: Lug Nut Sizes and Types (w/ Charts for Most Car Manufacturers)
Reasons Lug Nuts Won’t Come Off
The following are three common causes for a wheel lug nut refusing to come off. The lug nut or bolt may be:
Stripped or Rounded Off
In this case, use of an impact wrench or wrong size socket while installing a lug nut or bolt has rounded off (stripped) the hex-shape of the fastener. Or maybe it’s seized and your attempts to remove it with a lug wrench or socket have rounded it off.
In either case the fastener cannot be gripped such that it can be removed.
Read Also: What’s the Purpose of Wheel Spikes?
Seized
A zealous mechanic armed with an impact wrench may have over tightened one of the lug nuts on your car. Now it’s seized. It cannot be removed using the lug wrench that’s packed with your spare tire.
Rusted
The lug nuts and studs or bolts are severely rusted. This is common on older cars and cars that have been left unattended and uncovered in outdoor weather for many months. In this condition, the fastener also may be seized and just won’t turn.
Related: 5 Ways to Remove a Stubborn Bolt
How to Remove a Lug Nut That Won’t Come Off
Whether the lug nut is stripped, rounded-off, or seized due to either over tightening or corrosion, the loosening process will typically be the same except as noted below.
Begin with your car on the ground; not on jack stands or lifted up in any way. Make sure the transmission is set to Park or it’s in gear and firmly set the emergency brake. These steps will keep the wheels from rotating as you attempt to loosen the fasteners.
What You’ll Need
- Penetrating Oil (like WD-40 or Kano Aerokroil)
- Power drill (cordless or corded both work)
- 5/64″ and 7/64″ drill bits (cobalt bits work best)
- Drilling lubricant (ie: Three-in-One oil)
- Safety glasses
- 1/2″ drive 6-pt socket (of the correct lug nut size or slightly smaller)
- Lug nut extractor set (if needed)
- 1/2″ drive breaker bar
- Floor jack or 3-ft section of pipe (to slide over breaker bar)
Step 1 – Drill and Add Penetrating Oil
First, the nut and stud must be soaked with a penetrating oil. If the nut has a closed head, drilling that head can help get the oil into the threads.
To do this you will need high quality drill bits such as cobalt alloy steel drills in 5/64″ and 7/64″ diameters. Buy two of each since these small drills are very easy to break.
Drilling will be benefitted by the use of a lubricant. Three-in-One oil or equivalent will be adequate for this job. Also have a cup of cool water nearby. Now put on your safety glasses. Use a center punch and hammer to dimple the center of the lug nut.
Begin drilling with the smaller drill bit. Wet the tip of the bit with oil. Steady the drill motor with two hands. Drill at a very slow speed. Be careful to not bend the drill bit; this will break it pretty quickly.
Frequently stop drilling especially if the oil begins to smoke. Dip the hot bit in the water to cool it. Wipe away chips and reapply oil to the bit and hole. Repeat this process until the bit breaks through to the top of the stud.
Install the 7/64″ bit in the drill motor and repeat the above drilling procedure. Hold the drill motor firmly because the bit may want to suddenly grab in the hole and rotate the drill. Drill through again to the top of the stud.
You now have access to a reservoir for soaking the nut and stud with WD-40 or equivalent. Insert the WD-40 tube into the hole and wrap the tube at the nut surface with a shop (or paper) towel to catch any back spray. Squirt a bit of this lube into the hole.
Also spray WD-40 around the base of the lug nut. If time permits, allow the penetrating lube to soak overnight. It will then be more effective in freeing up the nut. Next morning add another squirt to the hole and base of the nut.
Corroded lug bolts will not benefit from the use of WD-40. With the wheel installed, the lug bolt threads are virtually inaccessible.
See Also: How to Remove a Stripped Oil Drain Plug
Step 2 – Use a “Snug” Socket or Lug Nut Extractor
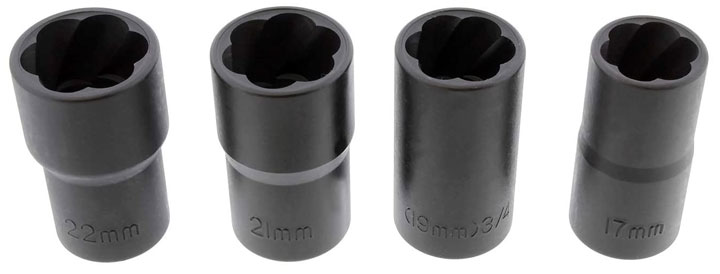
Select a 1/2″ drive 6 point socket that fits snugly on the nut or bolt. A deep socket may be required. A severely rusted fastener may be worn down such that a one size smaller socket (or smaller SAE equivalent for a metric lug nut; or smaller metric equivalent for an SAE lug nut) can be tapped on with a hammer.
Sometimes a one size smaller 12 point socket will tap into the rusted hex shape and grip pretty well.
If the nut or bolt head will not receive a conventional socket or is worn to a rounded shape, use of an extractor socket may be necessary. A suitable lug nut extractor set such as one by Irwin (best) or ABN (good) can be purchased online or at a quality auto parts store.
Use a socket size that is snug on the hex shape and hammer it in place. Using a short hardwood dowel against the socket while hammering can help you avoid striking your costly alloy wheel.
Step 3 – Loosen with Breaker Bar

Use a 1/2″ drive breaker bar that’s ideally 18″ to 24″ in length. Install it into the socket so that the handle extends horizontally and is in the position to be lifted upward to loosen the nut (if using a floor jack) or pushed downward (if not using a floor jack).
If Using a Floor Jack
Place your floor jack under the breaker bar handle and pump it up to lift the handle. You can generate up to one quarter of your car’s weight in pounds of force using this technique. Do keep your distance as the bar will bend and want to spring off the lug nut or off the lift pad of the floor jack.
Relate: How to Use a Hydraulic Floor Jack
If No Floor Jack is Available
If you have no suitable floor jack, you can apply considerable force to the breaker bar by sliding a pipe over the bar handle. The pipe should be slightly larger than the breaker bar to fit snugly. A three foot long pipe will work well for this.
Position the breaker bar so it is at an upward angle of about 10 degrees and to the left of the nut. You will be pushing downward to loosen the nut. Use your weight to apply force by carefully stepping onto the pipe.
Hold onto the side of your car to steady yourself. Use extreme caution to avoid slipping off the pipe or falling should the bar and socket pop off the lug nut or the nut suddenly break free.
You can reverse the bar position so that you must lift the pipe to turn the lug nut. Put on a pair of leather gloves to improve your grip. Note that lifting this way can be hard on your back so don’t overdo it. Also the pipe may bend so be cautious about the socket popping off the lug nut.
Step 4 – Finish Wheel Removal
Loosen the other lug nuts. Now you can jack the car up, properly support it and remove all the fasteners and then the wheel. Safe jacking procedures can be found HERE.
If All Else Fails…
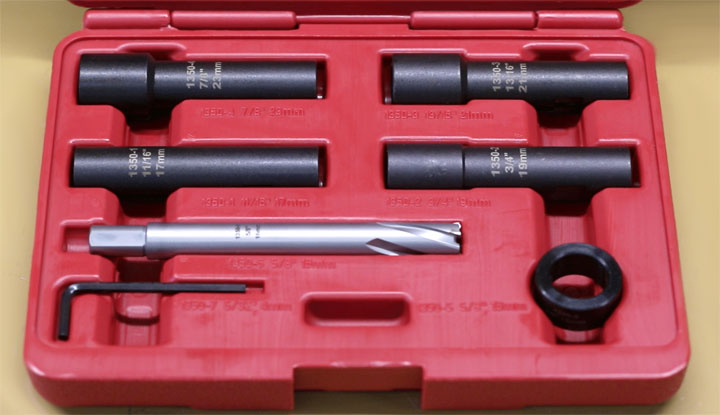
On rare occasion, the above fastener removal procedure will not get a lug nut or bolt off. If this should happen, a last ditch removal procedure is possible using a tool called the Lug Ripper.
To successfully use this tool will require you to precisely follow the manufacturer’s instructions at their website. Failure to do so can damage the tool rendering it unusable.
Be aware that this toolkit is not cheap. However, purchasing it may prove less expensive than taking your car to a qualified repair or tire shop for corrective action.
After successful removal of the stuck lug nut or bolt, you may choose to resell the Lug Ripper on Ebay, Craigslist, or local marketplace to recover much of the cost.
New Lug Nuts, Bolts and Studs
Following the removal of a seized or rusted lug nut or bolt, you should purchase and install new fasteners for the entire bolt pattern. Replacing just the damaged fastener could result in an out-of-balance condition.
Wheel studs that had seized or rusted lug nuts should be inspected.
- First, use a small wire brush first to clean the threads.
- Using a bright light, visually examine the threads. They should be clean, smooth and uniform in appearance.
- Run a new lug nut all the way onto the threads. It should spin on and off smoothly and easily by hand.
Any stud that displays damage and/or fails the inspection above should be replaced. If you are in any doubt about a stud’s condition, always replace it.
Did it all. The lug ripper literally ripped the lug nut in half. The other half is still seized in place. I think it literally welded itself to the rim with overheated breaks due to a seized caliper. Is this possible and do you have any recommendations. Thanks.
It would have to be really hot to weld to the stud. Have you tried hitting that lug nut with a powerful impact wrench?
Hi, take a small drill bit, like an 1/8″ or so, drill a few holes where the nut threads screwed onto the lug bolt. spray it with PB Blaster and retry to loosen with good 6 point socket.
Or drill into the center of the lug bolt with the small drill bit, then a larger drill bit, keep drilling into the bolt with a larger drill bit until you literally drill out the lug bolt, and the nut will fall off or you can break it off with by hitting it. You will have just destroyed you lug bolt this way. Disintegrated it. Success. Now you can remover the other lug nuts, remove the wheel, and replace the bad lug bolt with a new one. I have used this method many times. I you were removing a nut from a bolt and it was exposed more then you could just grind the whole nut off with an angle grinder, or file it off.
Those are good ideas. I would also consider replacing the stud after getting the lug nut off. The threads are probably going to be mangled and not something you would want to reuse.
Instead of drilling why not break off the stud by overtightening it? Might still need an extractor socket to grab the nut if it’s rounded off.
I personally wouldn’t do this, as overtightening could damage the rotor or hub assembly.
I once hammered a drill bit over the lug nut. The kind of drill bits you use for working on drilling door jambs and door knobs and stuff. This after a day of wd-40, using a cold chisel and everything else I could think of. I hammered the drill bit on pretty good. Smashed it on, set the drill on reverse and spun that sucker right off. Aluminum to aluminum seize from over tightening type situation. Avoidable. i took them all off after that & reinstalled all after that with anti seize. i put anti seize on the the lug, hand tightened it to evenly spread the anti seize. filled in any empty spots & lightly coated any surface of my aluminum rim that that touched my wheel hub. That was 4 Porsche 911’s ago. These days all rims are torued by hand. Porsche switched to lug lug bolts so I anti seize all of those once by hand.
Porsche 911s are great cars, and that is a clever solution.
Be aware that using anti seize will change your torque specs. Most torque specs are given dry, with no product on the fastener. You have to lower your torque by approximately 40% when you use anti seize. I personally avoid it where possible; I live in an area where rust is uncommon and I find I don’t really need to use anti seize at all. The risk of getting the torque spec wrong is greater than the risk of a stuck bolt for me.